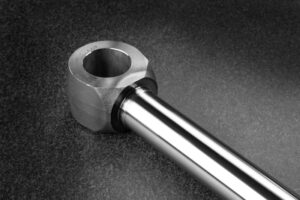
The Thompson PR direct drive series is specially designed to friction weld piston rods and cylinders for both OEM and Tier 1 manufacturers. These machines are used by many of the leading names in the yellow & green goods industry, cylinder manufacturing companies as friction welding is a repeatable, robust and accurate process.
Compared to conventional welding techniques, friction welding requires no consumables (gases and wire) or skilled operators.
The Thompson PR series is highly versatile, not only meaning pre-chromed piston rods, eyes and clevises, but also hydraulic cylinder caps and flanges can be joined on a single machine. The machines are easy-to-use, offering intuitive, tailor-made HMI process control software, wide range of flexible work holding solutions and variety of efficiency enhancements.
To download our piston rods and cylinders leaflet, go to our download centre.